炭素繊維RTM成形技術
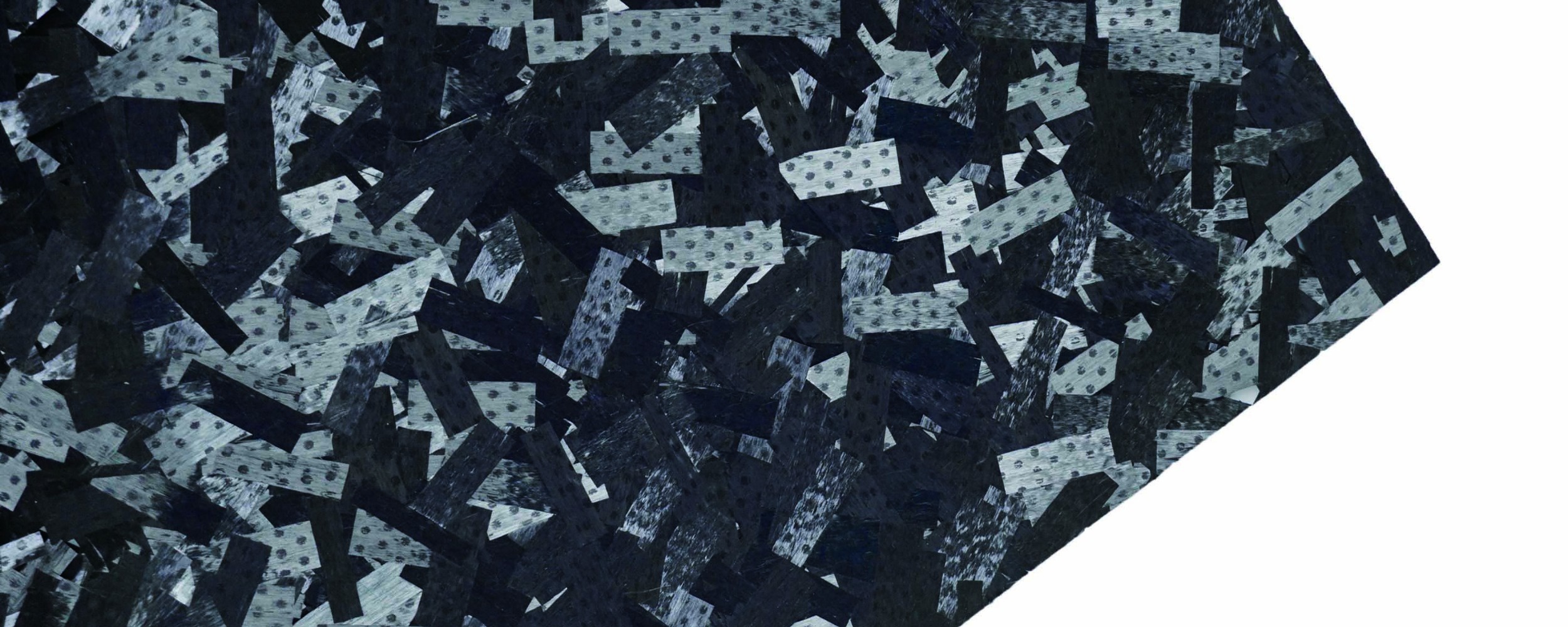
研究者 惣川 武勇
研究の背景
CFRPの実用化は近年、航空機分野での適用が大幅に進んでいるが、その実用化の多くが熱硬化性プリプレグを使用した成形方法であり、これは部材の成形に数時間から1日程度の時間がかかることから、年間数万台規模の量産を行う自動車分野では適用ができず、成形時間を数分レベルまで短縮させる高速成形法の開発が進められてきた。
そうした中、欧州の自動車メーカーのBMW社ではHP-RTM(高圧レジントランスファーモールディング)成形技術の開発により、CFRP部材の成形時間を10分以下に短縮することで量産車への適用を可能にし、2014年より販売を開始した電気自動車のi3の車体の主要骨格にCFRPを用いた量産化を実現している。
日本においても近年CFRPの車両部材への適用に向けた研究開発は活発となっている。これまでの研究では、例えば、平成20年度から実施された東京大学を中心としたNEDO事業の「サステナブルハイパーコンポジット技術の開発」では熱可塑性樹脂を用いたCFRPの中間基材のスタンパブルシートが提案されている。また、平成24年度から稼働した名古屋大学のナショナルコンポジットセンター(NCC)では炭素繊維の長繊維を利用した熱可塑性樹脂CFRPによる車両部材成形技術が提案されている。これらの熱可塑性樹脂をマトリックスとしたCFRPはスタンピングプレス成形により、RTMプロセスよりさらにサイクルタイムを短縮するのに有望であり多くの取組が見られるが、これまで適用されてきた熱硬化性CFRPとは成形方法に加え、強度や耐熱性、耐久性などの機械特性も全く異なるものであり実用化にはまだ多くの課題があると言える。
また、日本の複合材料産業の状況としては、炭素繊維の生産は世界の約7割を占める状況であるが、炭素繊維を使ったCFRPの生産は10%以下と非常に低い割合にとどまっており、川中から川下に至る基盤技術とサプライチェーンの形成が十分でなく、製造技術において欧米に大きく後れを取っている状況である。
こうした背景の中、直近の課題としては、まず欧米に後れを取ったRTM等の量産製造技術をキャッチアップし、そこへさらに日本の繊維技術、加工装置等の強みを活かした開発や、熱可塑性CFRPへの展開等を上乗せすることで日本の複合材料の産業力を強化させていくことが、産業界から強く求められている。
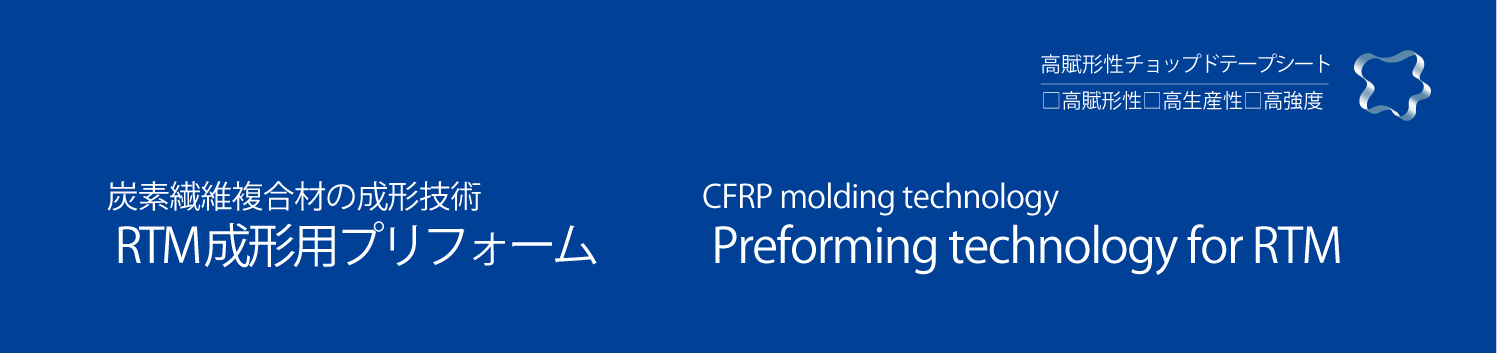
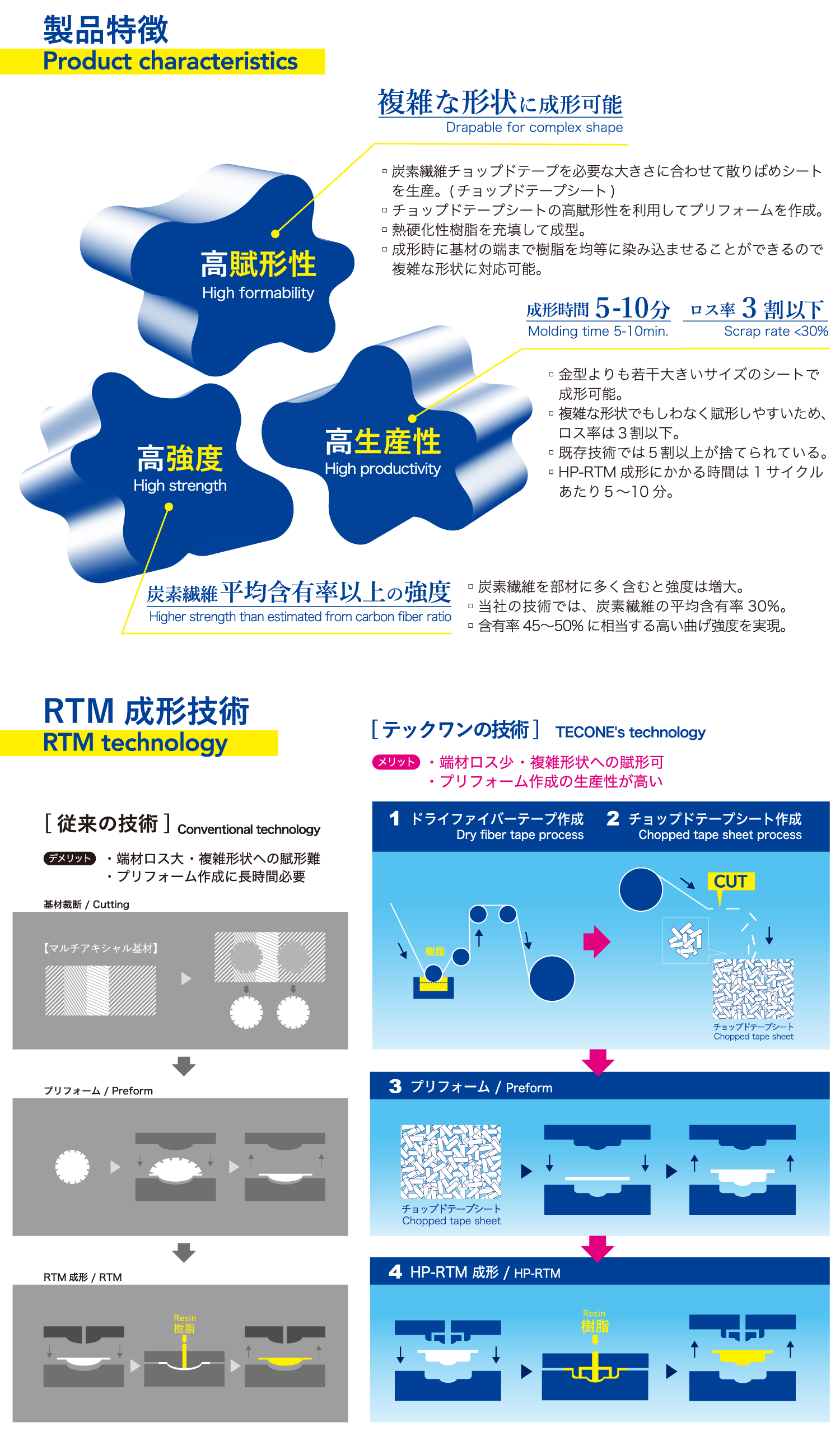
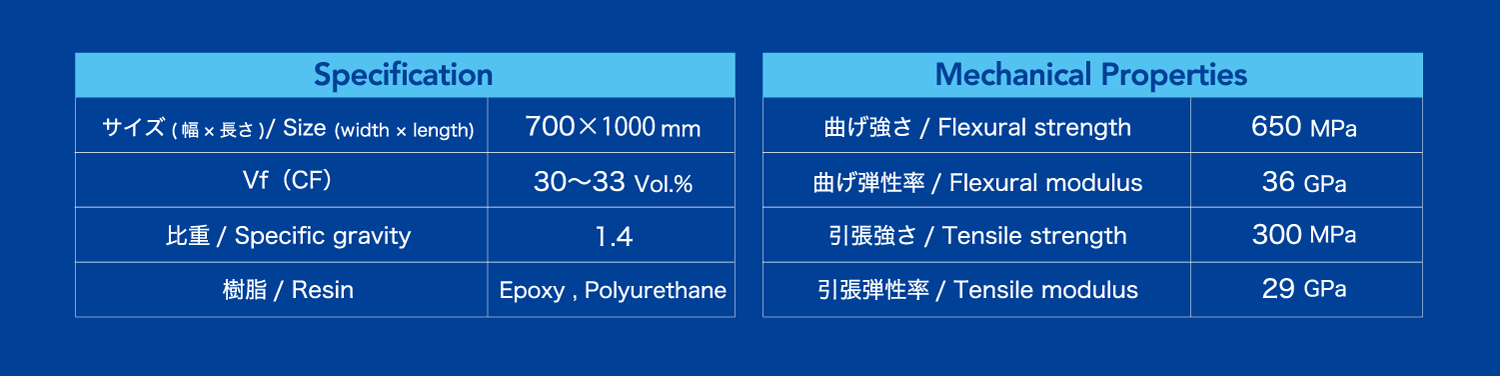
本プロジェクトは、共和工業株式会社、金沢工業大学、石川県工業試験場、石川県産業創出支援機構とテックワン株式会社が共同で実施しています。